X-RHex Key Features
X-RHex is designed to offer substantial improvements over its predecessors in terms of power, run-time, payload size, durability, and terrain negotiation, with a smaller volume and a comparable footprint and weight. Along with these advances, X-RHex incorporates a redesigned mechanical, electrical, and software architectures that are more reliable than past versions.
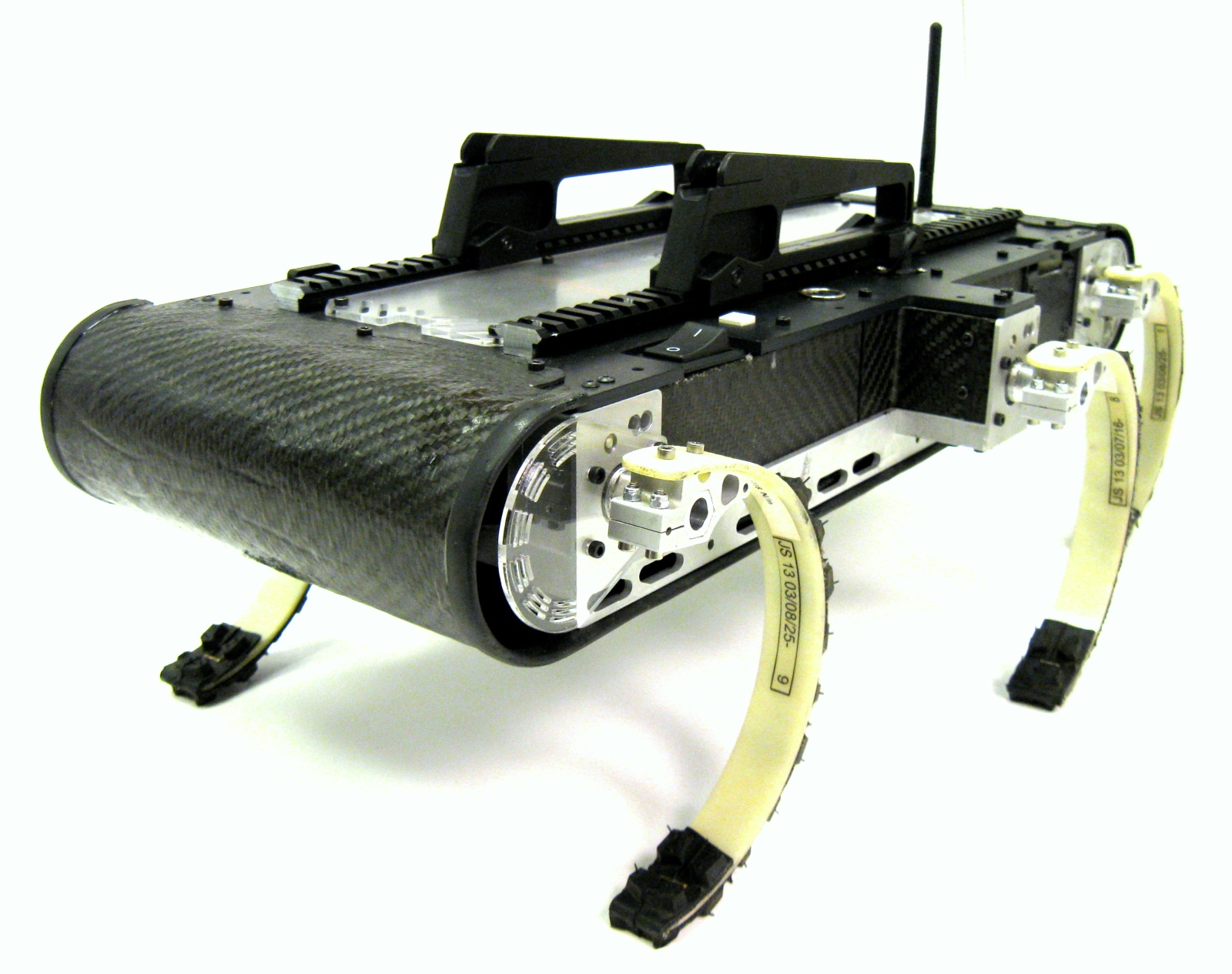
While only half the height and volume from the original RHex robot, X-RHex packs many improvements into its body. X-RHex’s motors provide twice the strength of the previous machine, while the battery allows for runtimes that triple and quadruple the original performance. Enabling this is a redesigned electronics architecture that supports high power Lithium Polymer batteries and features commercial off-the-shelf (COTS) motor controllers, while also providing an easy-to-use software interface. Along with these advances, X-RHex has a modular payload interfaces and a new flexible software system that allows rapid development of new sensors and behaviors.
More detailed information on the X-RHex design can be found in the X-RHex Technical Report (PDF).
Mechanical Design
The main objectives for the mechanical design of X-RHex were to improve frame durability (both in resistance to fatigue and impact) and overall robot serviceability while achieving similar or better performance to past robots. The overall dimensions (57×39×7.5 cm) were intended to maintain as much similarity to Research RHex (54×39×13.9 cm) as possible. Research RHex leg design was preserved, and since the leg mounts are nearly centered on an overall thinner body, the robot can operate with greater ground clearance even when in an inverted state. The motors were chosen after careful analysis of the performance of past RHex robots, and use a flat brushless model from Maxon Motor USA.
- Body dimensions: 57×39×7.5 cm
- Ground Clearance: 12.5 cm (12 cm when inverted)
- Leg Diameter: 17.5 cm
- Total Weight: 8.6 kg (9.5 kg with both batteries installed)
- Motor Continuous Power: 84 W
- Gear Ratio: 28:1
- Maximum Robot Power Density: 240 W/kg
Electronics
The electronics of X-RHex can be conveniently decomposed into four major subsystems: main computer, electronics stacks, batteries, motor assemblies. The main computer handles all high level control and communications. Each electronics stack contains three layers: motor controllers; a controller interface board which distributes power and communications to the motor controllers; and a battery management board responsible for power distribution, regulation, protection and monitoring. To the outer side of each stack, there is a lithium polymer battery and an interface board. Finally, there is a motor assembly containing a brushless motor and related sensors at each of the six hips.
- CPU Type: Intel Atom, 1.6 Ghz
- Communications Bus: USB
- Motor Controllers: Advanced Motion Controls DZRALTE-020L080
- Battery Type: 10 cell Lithium Polymer, hot swappable during robot operation
- Battery Capacity: 144 Wh
- Runtime: 90–180 min (typical usage)
Computation and Software
X-RHex makes use of a real-time software architecture to provide high frequency sensing and control, as well as network communication with the robot, on a near-stock Linux distribution. Our software architecture is based on a custom-developed open source package called Dynamism.
- Operating system: Linux (Ubuntu) with a Real-Time kernel
- Motor PD Loop speed: 20 khz (on the motor controller)
- Gait regulation speed: 300 hz (on the CPU)
- Communications: WiFi 802.11bg (internal) or other radio payload